Konecranes Remote Monitoring Services Help to Increase Reliability and Productivity
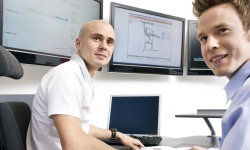
Gateshead, United Kingdom, May 06, 2009 --(PR.com)-- Konecranes, a global leader in the manufacturing of overhead lifting equipment, offers real-time remote monitoring services to capture critical production and crane usage data on demanding process cranes. Reliability and Productivity Services with remote monitoring can help to maximise uptime, increase safety, optimise performance, and achieve the highest lifecycle value of equipment. Remote monitoring allows for more accurate and in-depth analysis of crane usage that helps to reveal issues outside of standard maintenance checklists, including emerging deficiencies in processes, capacity, usage and overall operating efficiency.
Konecranes remote monitoring packages include reliability-based monitoring for more efficient troubleshooting and a more proactive productivity- and performance-based monitoring solution that ensures the highest level of crane availability with Global Technical Support (GTS). With more than 350,000 cranes under service contracts worldwide, Konecranes is able to apply its unique knowledge and resources to develop innovative solutions that improve crane reliability and performance.
The Konecranes remote monitoring system sends around-the-clock crane usage data via advanced connections to Konecranes GTS centres located in the United States, Finland and China. The main fixed connection and a secondary wireless connection (i.e. 3G, GPRS or satellite), attached to the crane, transfer information through a secure VPN on a redundant w24 router. In addition, some processed data can be integrated with the customer's IT system.
Reliability remote monitoring services capture crane usage data through continuous monitoring. As maintenance issues arise, customers and service technicians can troubleshoot more efficiently with faster response times and resolutions. Maintenance services can be performed based on the actual usage data of cranes. Reliability monitoring tracks usage trends, including unsafe or improper crane usage, which might not be detected during standard, periodic maintenance inspections. Downtime can be minimised or prevented using the fault histories generated through remote monitoring to predict emerging technical and mechanical problems. Optional improvement reports are also available for planning predictive maintenance.
The advanced Productivity remote monitoring services provide real-time data that is monitored online by skilled engineers to enable higher crane availability, optimal Overall Equipment Efficiency (OEE), informed lifecycle planning and continual customer process improvement. Konecranes engineers use state-of-the-art technology and software at the GTS centres to locate and predict maintenance needs and other critical issues, including production-related process problems. Recommended improvements can be put into action within the same work shift, if appropriate. Problems can also be proactively identified using the simple, graphic interface that is available online. In order to help determine the customer's competitive position, productivity and performance-based monitoring also benchmarks actual crane OEE performance with the customer's other cranes or with industry standards.
Optional productivity and performance-based services are available, including production and working cycle analysis. The historic and predictive production and working cycle analyses gained from remote monitoring services can be used to optimise production processes and achieve the highest lifecycle value of the equipment. With increased production efficiency, a more competitive pricing strategy can be offered. Remote monitoring services also offer optional remote support for start-up and commissioning phases.
To find out more about Reliability and Productivity Services with remote monitoring, or for other lifting solutions and services, contact Konecranes Service Ltd., Unit 19 Princes Park, Fourth Avenue, Team Valley, Gateshead, NE11 0LQ, by phone +44 1914 873898, or by fax +44 1914 872625.
Further information: James Bow, Marketing Manager, Konecranes Service Ltd., Phone: +44 1914 873898, or visit www.konecranes-uk.com
Konecranes is a world-leading group of Lifting Businesses, serving a broad range of customers, including manufacturing and process industries, shipyards, ports and terminals. Konecranes provides productivity-enhancing lifting solutions as well as services for lifting equipment and machine tools of all makes. The Group has 9,900 employees, at more than 485 locations in 43 countries.
###
Konecranes remote monitoring packages include reliability-based monitoring for more efficient troubleshooting and a more proactive productivity- and performance-based monitoring solution that ensures the highest level of crane availability with Global Technical Support (GTS). With more than 350,000 cranes under service contracts worldwide, Konecranes is able to apply its unique knowledge and resources to develop innovative solutions that improve crane reliability and performance.
The Konecranes remote monitoring system sends around-the-clock crane usage data via advanced connections to Konecranes GTS centres located in the United States, Finland and China. The main fixed connection and a secondary wireless connection (i.e. 3G, GPRS or satellite), attached to the crane, transfer information through a secure VPN on a redundant w24 router. In addition, some processed data can be integrated with the customer's IT system.
Reliability remote monitoring services capture crane usage data through continuous monitoring. As maintenance issues arise, customers and service technicians can troubleshoot more efficiently with faster response times and resolutions. Maintenance services can be performed based on the actual usage data of cranes. Reliability monitoring tracks usage trends, including unsafe or improper crane usage, which might not be detected during standard, periodic maintenance inspections. Downtime can be minimised or prevented using the fault histories generated through remote monitoring to predict emerging technical and mechanical problems. Optional improvement reports are also available for planning predictive maintenance.
The advanced Productivity remote monitoring services provide real-time data that is monitored online by skilled engineers to enable higher crane availability, optimal Overall Equipment Efficiency (OEE), informed lifecycle planning and continual customer process improvement. Konecranes engineers use state-of-the-art technology and software at the GTS centres to locate and predict maintenance needs and other critical issues, including production-related process problems. Recommended improvements can be put into action within the same work shift, if appropriate. Problems can also be proactively identified using the simple, graphic interface that is available online. In order to help determine the customer's competitive position, productivity and performance-based monitoring also benchmarks actual crane OEE performance with the customer's other cranes or with industry standards.
Optional productivity and performance-based services are available, including production and working cycle analysis. The historic and predictive production and working cycle analyses gained from remote monitoring services can be used to optimise production processes and achieve the highest lifecycle value of the equipment. With increased production efficiency, a more competitive pricing strategy can be offered. Remote monitoring services also offer optional remote support for start-up and commissioning phases.
To find out more about Reliability and Productivity Services with remote monitoring, or for other lifting solutions and services, contact Konecranes Service Ltd., Unit 19 Princes Park, Fourth Avenue, Team Valley, Gateshead, NE11 0LQ, by phone +44 1914 873898, or by fax +44 1914 872625.
Further information: James Bow, Marketing Manager, Konecranes Service Ltd., Phone: +44 1914 873898, or visit www.konecranes-uk.com
Konecranes is a world-leading group of Lifting Businesses, serving a broad range of customers, including manufacturing and process industries, shipyards, ports and terminals. Konecranes provides productivity-enhancing lifting solutions as well as services for lifting equipment and machine tools of all makes. The Group has 9,900 employees, at more than 485 locations in 43 countries.
###
Contact
Konecranes Service Ltd.
James Bow
44 1914 873898
http://www.konecranes-uk.com
James Bow
44 1914 873898
http://www.konecranes-uk.com

Categories