Crystallcut Update Polyester Congress
Kreyenborg Group’s BKG - Underwater Pelletizer systems (www.bkg.de) today presented an update on their innovative Crystallcut Underwater Pelletizing process, at the worlds leading Global conference for the Polyester Industry, the Polyester Congress organized by Maack Business Services. (www.mbspolymer.com)
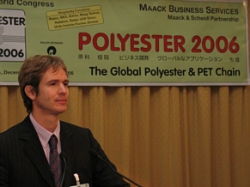
Munster, Germany, December 16, 2006 --(PR.com)-- David Bargery Sales Manager for the Kreyenborg Group described to the audience, of more than 500 industry experts, how the Crystallcut technology has evolved from a lab-scale development in the company’s trial facilities, in Muenster-Germany, to become the leading pelletizing technology for the Global Polyester industry.
The Crystallcut process is unique in the fact that it utilizes the heat inherently within the polymer melt to crystallize the pellets within the BKG underwater pelletizing process.
The polymer is cut underwater directly at the pelletizer die face, transported to a centrifugal pellet dryer where the water is separated and the polymer dried. The material exits the pellet dryer and is conveyed on a specially designed vibratory conveyor where the conversion from amorphous to crystallized material occurs. This complete process utilizes the heat already inside the pellet, thus avoiding the need for any further energy input. This is a dramatic advancement for the Polyester Industry and the technology is being widely applied worldwide.
The diverse applications, that the Crystallcut technology can be applied to range from small scale extrusion and recycling, through to world-scale polyester production plants. The hot pellets are conveyed directly from the Crystallcut process to a Solid State Polymeriser, with significant energy savings due to minimal additional energy being required to heat the pellets up in the SSP.
In Polyester production the technology can be utilized to directly convey the pelletized material to existing SSP process, or for direct pellet production to high iv (intrinsic viscosity) processes that can completely eliminate the costly SSP stage.
During the PET Congress, David Bargery stated, "The Crystallcut Development has progressed a long way since the early days in our trial facility. We now have a truly innovative technology in operation at major customers all over the world. From small scale PET recycling applications right through to world scale polymer plants."
BKG also announced the successful startup of its new Crystallcut technology within Eastman Company’s recently completed IntegRex™ technology based manufacturing process in Columbia, South Carolina, USA.
The BKG Crystallcut process can provide considerable energy savings that were highlighted during the presentation at the Amsterdam Congress. Copies of the presentation are available from BKG. www.bkg.de
###
This press release issued by REGIS solutions partner to BKG and the Kreyenborg Group.
The Crystallcut process is unique in the fact that it utilizes the heat inherently within the polymer melt to crystallize the pellets within the BKG underwater pelletizing process.
The polymer is cut underwater directly at the pelletizer die face, transported to a centrifugal pellet dryer where the water is separated and the polymer dried. The material exits the pellet dryer and is conveyed on a specially designed vibratory conveyor where the conversion from amorphous to crystallized material occurs. This complete process utilizes the heat already inside the pellet, thus avoiding the need for any further energy input. This is a dramatic advancement for the Polyester Industry and the technology is being widely applied worldwide.
The diverse applications, that the Crystallcut technology can be applied to range from small scale extrusion and recycling, through to world-scale polyester production plants. The hot pellets are conveyed directly from the Crystallcut process to a Solid State Polymeriser, with significant energy savings due to minimal additional energy being required to heat the pellets up in the SSP.
In Polyester production the technology can be utilized to directly convey the pelletized material to existing SSP process, or for direct pellet production to high iv (intrinsic viscosity) processes that can completely eliminate the costly SSP stage.
During the PET Congress, David Bargery stated, "The Crystallcut Development has progressed a long way since the early days in our trial facility. We now have a truly innovative technology in operation at major customers all over the world. From small scale PET recycling applications right through to world scale polymer plants."
BKG also announced the successful startup of its new Crystallcut technology within Eastman Company’s recently completed IntegRex™ technology based manufacturing process in Columbia, South Carolina, USA.
The BKG Crystallcut process can provide considerable energy savings that were highlighted during the presentation at the Amsterdam Congress. Copies of the presentation are available from BKG. www.bkg.de
###
This press release issued by REGIS solutions partner to BKG and the Kreyenborg Group.
Contact
Regis Kreyenborg
David Bargery
+441243 825661
www.bkg.de
David Bargery
+441243 825661
www.bkg.de

Categories