Innovative Process to Smooth Helicopter Ride and Reduce Overall Aircraft Vibration
Accurate prediction of rotating components behavior during flight in helicopter is a huge boost to the industry in safety, time and money
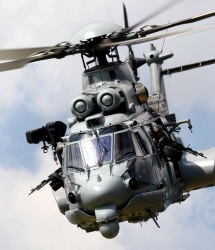
New York, NY, December 29, 2012 --(PR.com)-- One of the largest “big ticket” items faced by the helicopter maintenance industry today is the issue of rotor track and balance (RT&B). If there were a way to make the process of rotor track and balance more efficient it would be a huge boost to the helicopter operator, saving both time and money.
While current systems use a slightly different approach to balance the rotors, each has essentially the same goal ─ to reduce the destructive vibrations induced to the helicopter structure from the main and tail rotor. It requires commitment of extensive time and money to ensure the smoothing of an aircraft on a regular basis.
On average, 70% of the RT&B process requires 2 to 5 test flights in order to successfully balance the rotors to vibration levels below acceptable limits, using systems in the market place today. The remaining 30% are conditions that current systems are not programmed to solve and sometime require more than 10 test flights (trial and error), replacement of dynamic components, guesswork and other costly maintenance action in order to change the dynamic profile of the vibration reading due to lack of technology.
Safety concerns, high maintenance time, high fuel costs, and operational unavailability of the aircraft are some of the reasons why a more advanced and more efficient method of smoothing should be available and employed by helicopter operators.
Shake’d Technologies, Inc., a New York based firm engaged in the development, delivery and support of advanced rotary wing technologies, developed a unique method to dramatically improve the RT&B balancing process which results in more accurate balancing adjustments, the first time, on the ground, without the needs for additional reference test flights.
“There is an excellent agreement between the predicted and measured vibration values still meeting all RT&B tolerance limits for vibration as designated by the OEM in the required flight regimes without the need for additional reference flights,” said Eli Navon, CEO of Shake’d Technologies, Inc.
“Current systems in the marketplace are not programmed to consider the behavior of components in certain flights conditions,” said Eli Navon. “For example; current systems check for vibration data while aircraft is in forward flight in different speeds and hover, (as required by OEM) but none of the solutions consider vibration inspection during other critical flight conditions such as climbing, descending, banking with power, and gross weight variations. (very heavy vs. very light). Any experienced helicopter pilot will tell you that helicopters vibrate more during descent then during forward flight,” said Eli Navon. The New CDB system considers all these flight conditions during the balancing process on the ground.
“We did CDB on two of our Apaches, AH-64A 120 and AH-64D 006. I have flown both and can tell you that it has made an obvious difference. Not only the vibrations are way down, it seems that the noise in the cockpit is quieter,” said Craig Ernst, Experimental test pilot at the Aviation Technologies Directorate (ATD).
“The system is fully developed and it is already deployed and operational,” said Eli Navon. “The Israeli Air force are using the technology on the CH-53 aircraft and already seeing great results in avoiding unnecessary test flights, removal of technician guesswork for troubleshooting, avoiding unnecessary part replacement, and increasing mission readiness. Pilots report on increase of overall aircraft efficiently in higher take off weight (more collective) and longer/extended range.”
“Because of the unique and efficient method of CDB algorithms, the system is able to examine and predict main rotor components failure and alert the operator before the test flight,” said Eli Navon. “The health of components such as blades, dampers, bearings and swashplate are examined during the balancing process.”
The CDB process takes less than two hours and it is utilizing industry standard standalone ground unit equipment. The technology is transferable and can be integrated (in part or in full) with current balancing systems in the market place today.
While current systems use a slightly different approach to balance the rotors, each has essentially the same goal ─ to reduce the destructive vibrations induced to the helicopter structure from the main and tail rotor. It requires commitment of extensive time and money to ensure the smoothing of an aircraft on a regular basis.
On average, 70% of the RT&B process requires 2 to 5 test flights in order to successfully balance the rotors to vibration levels below acceptable limits, using systems in the market place today. The remaining 30% are conditions that current systems are not programmed to solve and sometime require more than 10 test flights (trial and error), replacement of dynamic components, guesswork and other costly maintenance action in order to change the dynamic profile of the vibration reading due to lack of technology.
Safety concerns, high maintenance time, high fuel costs, and operational unavailability of the aircraft are some of the reasons why a more advanced and more efficient method of smoothing should be available and employed by helicopter operators.
Shake’d Technologies, Inc., a New York based firm engaged in the development, delivery and support of advanced rotary wing technologies, developed a unique method to dramatically improve the RT&B balancing process which results in more accurate balancing adjustments, the first time, on the ground, without the needs for additional reference test flights.
“There is an excellent agreement between the predicted and measured vibration values still meeting all RT&B tolerance limits for vibration as designated by the OEM in the required flight regimes without the need for additional reference flights,” said Eli Navon, CEO of Shake’d Technologies, Inc.
“Current systems in the marketplace are not programmed to consider the behavior of components in certain flights conditions,” said Eli Navon. “For example; current systems check for vibration data while aircraft is in forward flight in different speeds and hover, (as required by OEM) but none of the solutions consider vibration inspection during other critical flight conditions such as climbing, descending, banking with power, and gross weight variations. (very heavy vs. very light). Any experienced helicopter pilot will tell you that helicopters vibrate more during descent then during forward flight,” said Eli Navon. The New CDB system considers all these flight conditions during the balancing process on the ground.
“We did CDB on two of our Apaches, AH-64A 120 and AH-64D 006. I have flown both and can tell you that it has made an obvious difference. Not only the vibrations are way down, it seems that the noise in the cockpit is quieter,” said Craig Ernst, Experimental test pilot at the Aviation Technologies Directorate (ATD).
“The system is fully developed and it is already deployed and operational,” said Eli Navon. “The Israeli Air force are using the technology on the CH-53 aircraft and already seeing great results in avoiding unnecessary test flights, removal of technician guesswork for troubleshooting, avoiding unnecessary part replacement, and increasing mission readiness. Pilots report on increase of overall aircraft efficiently in higher take off weight (more collective) and longer/extended range.”
“Because of the unique and efficient method of CDB algorithms, the system is able to examine and predict main rotor components failure and alert the operator before the test flight,” said Eli Navon. “The health of components such as blades, dampers, bearings and swashplate are examined during the balancing process.”
The CDB process takes less than two hours and it is utilizing industry standard standalone ground unit equipment. The technology is transferable and can be integrated (in part or in full) with current balancing systems in the market place today.
Contact
Shake'd Technologies, Inc
Eli Navon
(646) 747-5592
www.cdbdata.com
Eli Navon
(646) 747-5592
www.cdbdata.com

Categories